The quick and dirty definition of a chronometer is an extremely accurate time piece, right? But how accurate is accurate? Well, the chronometer as we know it today grew out of the pursuit of a solution to the problem of determining longitude at sea. That solution, it turned out, was to know when it was noon at your location on the open ocean and, simultaneously knowing what time it was in Greenwich, England (hence, the use of GMT). Use simple arithmetic to find the time difference and you could figure out how far west or east you were. That’s longitude. (North and south was figured by sighting the North Star at night – a task quite separate from time measurement. )

But knowing the time in Greenwich was the rub. You needed a clock on board your ship that was set to Greenwich time. OK, that’s easy enough. You set the special clock to Greenwich time before you leave England. But how do you know that clock isn’t running slow or fast? Well, you have to trust to the accuracy of said clock. And that’s where chronometers come in.
We won’t go into the technical details of what John Harrison did to design a clock good enough to ultimately won the Longitude Prize, but win it he did.
And now Contrôle Officiel Suisse des Chronomètres, or COSC, the Official Swiss Chronometer Testing Institute, is the organization which handles certifying the accuracy and precision of wristwatches in Switzerland – and by extension, the world.
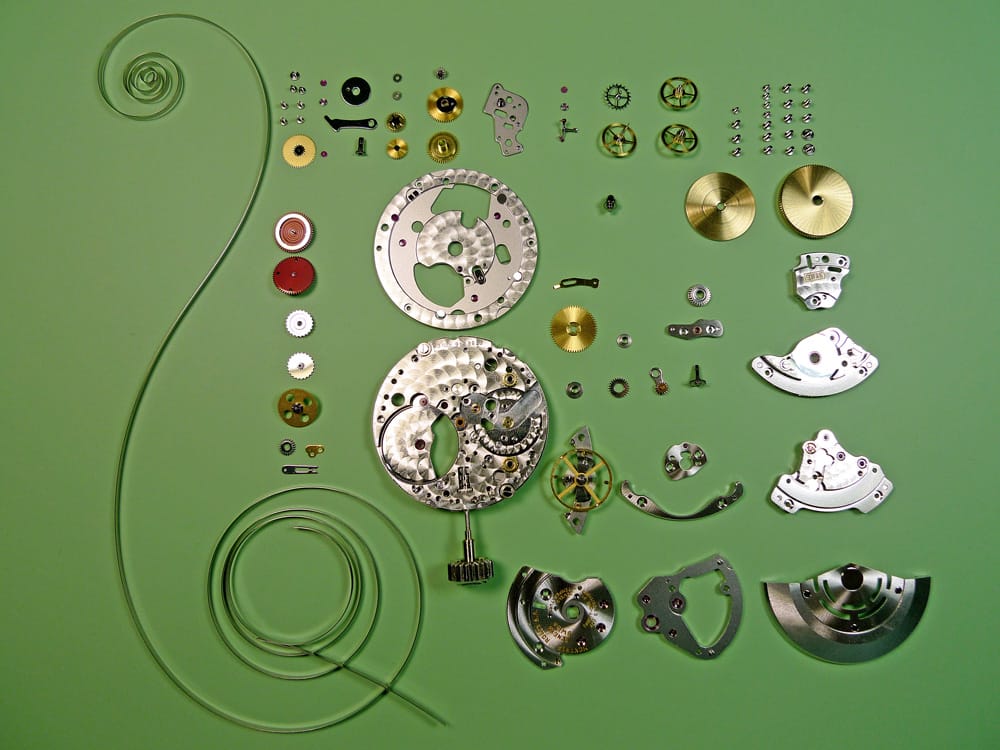
Basically, a movement that’s been certified by COSC and achieved chronometer status is accurate to -4/+6 seconds per day. But there’s a little more to it than that.
The testing it takes to achieve a COSC certificate is based on ISO standard 3159. A movement is tested over fifteen days, in five positions, at three different temperatures. Measurements are made each day, and are compared to two atomic clocks. The standards for achieving a chronometer certificate are as follows:
- An average daily rate of -4/+6 seconds for the first ten testing days (certain tests are performed on certain days),
- A mean (or average) variation in rate of no more than 2 seconds per day,
- A variation in rates of no more than 5 seconds between any two days’ readings,
- A difference between rates in the horizontal and vertical positions of no more than -6/+8 seconds
- The largest variation in rates must be no more than 10 seconds
- The thermal variation in rate can be no more than ±0.6 second per degree
- The difference between the average mean daily rate of the first two days of testing from the mean daily rate of the last test day can be no more than ±5 seconds
And now you see, it’s a little more involved than simply -4/+6 seconds per day.
And to achieve this kind of performance, there are numerous physical effects and circumstances that need to be mitigated, avoided, or overcome, with regard to individual components and their assembly.
Temperature effects include viscosity changes in lubricants, and thermal growth or shrinkage of component parts.
The dimensions of each component need to be controlled. Design tolerances – the degree to which each piece part is dimensionally identical to its siblings in a manufacturing lot, and to the original design dimensions – must be maintained. This also relates to how each component mates to the parts it interacts with.
Misalignment of mating pieces – say a pivot in a jewel, or (getting technical here) a third wheel to third wheel pinion to fourth wheel – must be eliminated. At a minimum, such misalignments will cause an increase in friction. At worst, they’ll cause interference and binding between parts.
And components that are not intended to directly interact, must never inadvertently touch each other. And it should go without saying that there can’t be any foreign matter floating around the movement.

After all that is properly accounted for, there are still going to be infinitesimal differences in the build of each movement. These are due both to infinitesimal differences in the individual components used to build each movement, and minute differences in alignments – even with locating pins and shoulders.
These small differences are enough to cause differences in how each movement runs before adjusting. And so, a watchmaker is needed to make those final adjustments and bring the movement into spec so it can pass the COSC tests. That’s where – surprise! – the words, “Adjusted in five positions” comes from on Rolex movements.
And so, even with the marvels of modern manufacturing, you can see how making and adjusting a watch movement with over 200 parts to perform within seconds per day is no small feat.